Bagh, a picturesque village in the heart of India, Madhya Pradesh, is renowned for its exquisite block printing technique to make Bagh prints. This remarkable craft takes its name from the meandering River Baghini, which gracefully flows through the village, symbolising the very essence of this art form. Bagh Prints of Madhya Pradesh is an extraordinary display of vibrant floral and geometric patterns, meticulously created using intricately carved wooden blocks and natural vegetable dyes.
Bagh Prints’ History and Story of Ismail Suleman Khatri
Block printing in India is an ancient art that dates back to 3000 BC, possibly originating in the Indus Valley Civilization. Some historians believe that India may have been the birthplace of textile printing. Archaeological evidence from Mohenjedaro reveals the knowledge of complex mordant dyeing techniques in the subcontinent since the second millennium BC. The craft of block printing was practised by a group known as ‘Chhipas’ or ‘Bhavsars’ in places like Kukshi, Dharampuri, and Thikri.
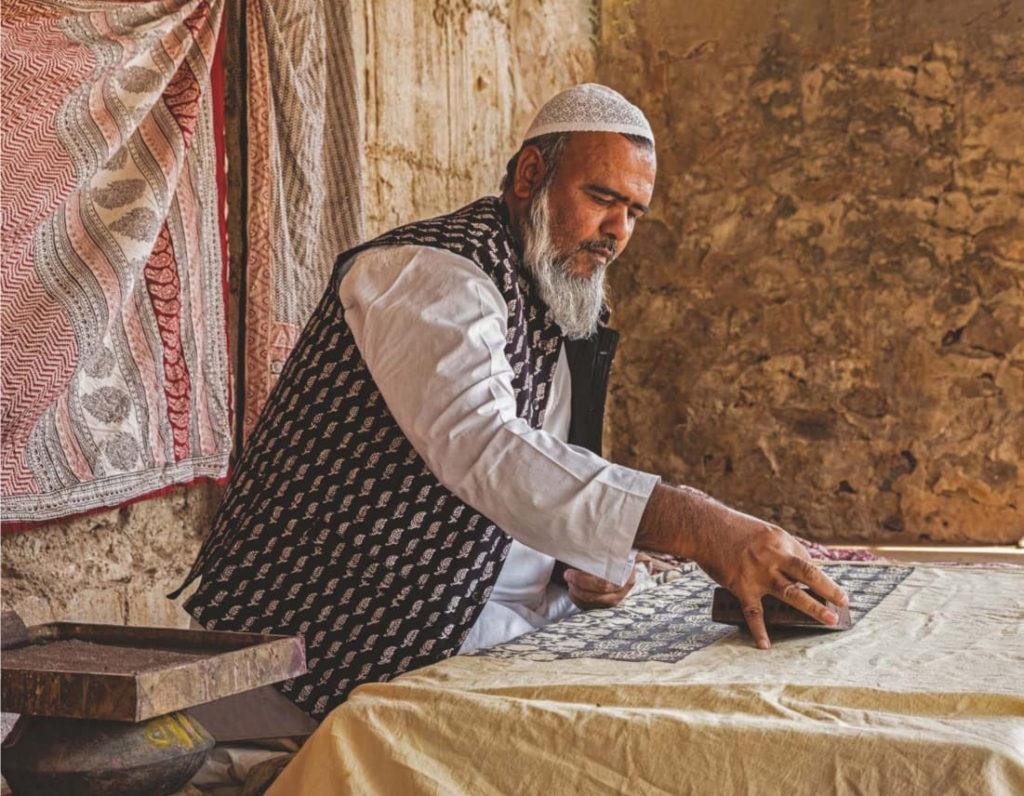
The origin of the term ‘Bagh’ carries various narratives. One story links it to the ancient ‘Bagh Gupha,’ Buddhist caves discovered in 1818 AD. Over time, as tigers or ‘Bagh,’ roamed the dense forests surrounding the caves, the name stuck. Another tale connects Bagh and Kutch, suggesting a shared lineage between the Khatris who settled in these regions. The resemblance in their crafts, processes, and materials further strengthens this connection.

The textile community called ‘Khatris’ migrated from Sindh to Gautampura and later settled in Manavar. A portion of the Khatri clan moved to Bagh, in search of quality water for their craft and to avoid taxes. In 1960, Ismail Suleman Khatri discovered that the high copper content in the Baghini river water enhanced the richness of colours, marking a turning point in Bagh block printing’s history. A devoted artisan with a generous spirit, Mr Khatri has made significant strides in advancing Bagh prints by personally sponsoring training programs and providing sustainable livelihoods to over 2500 individuals from marginalised communities.
Bagh’s Purpose in the Community and Its Evolution
The tribal communities of Dhar hold the Bagh print in high regard, embracing its cultural and religious significance. They utilise the traditional Bagh prints in vibrant red, black, and white hues, adorned with religious motifs, for significant festivals and momentous occasions such as weddings. During marriage ceremonies, the groom’s family presents the bride’s family with Bagh print dresses, including the ‘Lugda’ (head draping garment) and ‘Ghaghra’ (long skirt), accompanied by silver jewellery.
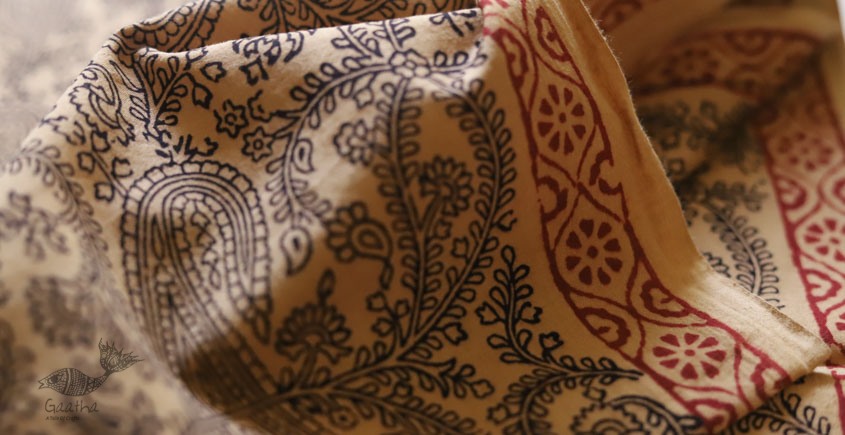
Bagh print fabric is extensively used in local tribes’ religious ceremonies, incorporating sacred Bagh print motifs like cows and elephants. Spearheaded by the visionary Ismail Khatri, the craftsmen have evolved and diversified the art form, resulting in the popularity and versatility of Bagh print dresses. Traditionally, women wore Bagh-printed lehengas and ghagras. Over time, the traditional attire transformed into Bagh print sarees, salwars, dupattas, scarves, and even t-shirts. However, the options for contemporary men’s wear are limited to scarves and Handkerchiefs, unlike the traditional turbans and lungis adorned with Bagh prints. The fabric has also become a common feature in traditional households, which boast of Bagh print curtains, bed covers and cradle linings due to its light and cooling properties. Nowadays, Bagh print has expanded its applications to include curtains, lampshades, screens, cushion covers, and wall pieces.
The Production of Bagh Print Dresses
The immaculate art of Bagh block printing is still intact. Upon visiting, one may admire the traditional way, talented artisans create magic in the form of Bagh print suits or sarees. The production of Bagh print suits in Bhopal comprises the following steps.
1: Carving The Wooden Printing Block
It all starts with the intricately carved wooden block. Printers highly value their printing blocks laced with Bagh print motifs, and the Khatris meticulously preserve both active and old blocks as design treasures. The teak block is smoothed using carpentry tools and coated with white primer. The craftsman skillfully engraves intricate designs onto the block using sharp tools. To verify the design, a print is taken on paper. The block is then immersed in oil for a few days, safeguarding it from warping and insects, which is crucial due to its exposure to water-based dyes.
.jpg)
2: Preparing the Cloth
The Bagh print dress material is processed in copper tubs, washed, and sun-dried. The dry fabric is then immersed in a mixture of castor oil and goat droppings, which interact to generate heat, enhancing absorbency. Through foot-pressing, the cloth passes through this solution, creating froth. It is subsequently dried and soaked in a starch solution containing herbal powders, followed by another round of sun-drying. Shade drying is crucial to maintain the desired yellow colour, preventing it from becoming too green in the sun.
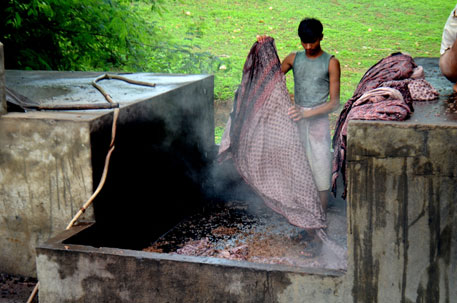
3: Printing the Cloth
A filtered paste made by mixing the dye with ‘dhavda’ gum and filtering the mixture is poured inside a wooden tray. There are two types of pastes — red and black. The wooden blocks take the dye by pressing against it on the tray. The yellowish cloth from the earlier process is a canvas for the craftsman, who skillfully prints the designs. The printer starts printing the fabric from the edge carefully moving inwards. To avoid overlapping on the corners of the cloth, they put an old cloth or paper on the part, where the printing has already been done. As a final step, the Bagh print dress material undergoes washing and drying once again.
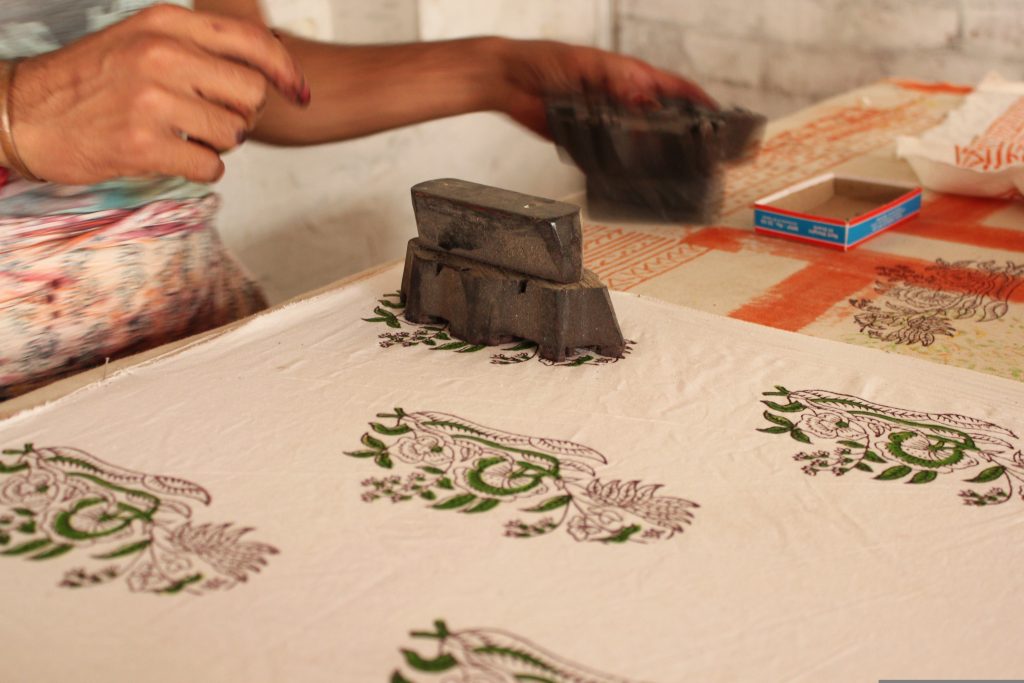
4: Printed Cloth is Dyed
To achieve the distinctive contrast and finishing of the Bagh print kurta, it undergoes an additional dyeing process. Alizarin and ‘dhavadi’ flowers are boiled in a large copper container concealed within a cement structure. The printed fabric is then boiled in this solution for several hours, resulting in the desired red and white areas. Once all of this is achieved, the cloth is hung out to dry in the sun.
Bagh Print Frock Design
The Bagh print suits in Bhopal boast intricate and abstract Bagh print motifs of floral designs, surpassing even the ones found in Rajasthan. Bagh prints are distinguished by multiple rows of meticulously crafted geometric patterns, predominantly in red and black hues. Alizarin is employed to obtain the vibrant red colour, while black is achieved through fermenting iron filings in jaggery. The main Bagh print kurti design template consists of four elements: ‘nariyal’ (coconut shape), ‘tikona’ (triangles forming a peak), ‘gehwar’ (fan-like shape), and ‘lehar’ (waves), collectively known as a ‘parivar’ (family).
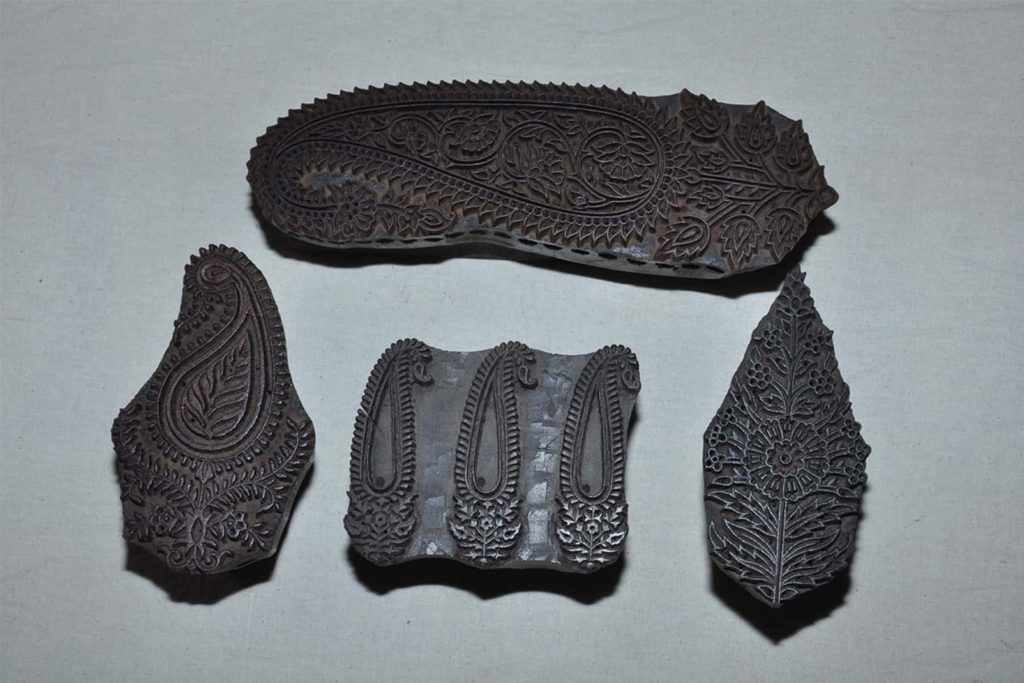
Traditional Bagh print motifs such as the ‘Nandana’ mango, ‘Tendu’ plant, ‘Mung Ki Phali,’ ‘Khirali Keri,’ ‘Leheria,’ ‘Jowaria,’ and ‘Phool Buta’ adorn the fabric. The fabric borders, reminiscent of the stone carvings in the Bagh Caves, are inspired by ‘Bel,’ the climbing creeper plant. This craft offers immense flexibility, allowing for the creation of countless surface designs through combinations of borders, motifs, and floral nets.
Can Bagh Prints Survive In Our Times?
While industrially produced Bagh print fabric is now prevalent for everyday wear, Bagh prints continue to be cherished for major festivals and ceremonies. As the global market recognizes the value of hand-block printed fabrics, Bagh artisans have embraced contemporary trends, incorporating an array of colours and patterns into their prints. This age-old technique of hand-block printing is primarily practised on cotton fabric, while also being applied to materials such as silk, chiffon, jute, ‘Maheshwari,’ and ‘Chanderi’ silk.
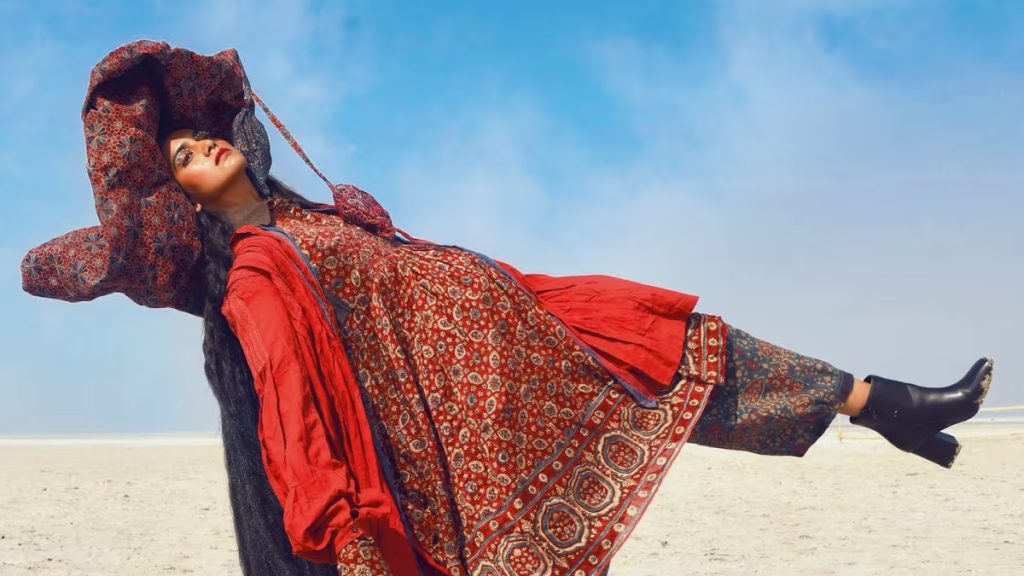
Despite facing challenges and threats over the years, this ancient craft has persevered and evolved, thanks to the unwavering dedication of skilled artisans and their commitment to preserving tradition while embracing contemporary sensibilities. Renowned as award-winning artisans, the late Ismail Suleiman Khatri and his wife Hajjani Jetun Bi played a pivotal role in preserving the printing tradition in Bagh. Their five sons, equally skilled ‘karigars’, have continued the practice, adapting designs to suit modern aesthetics.
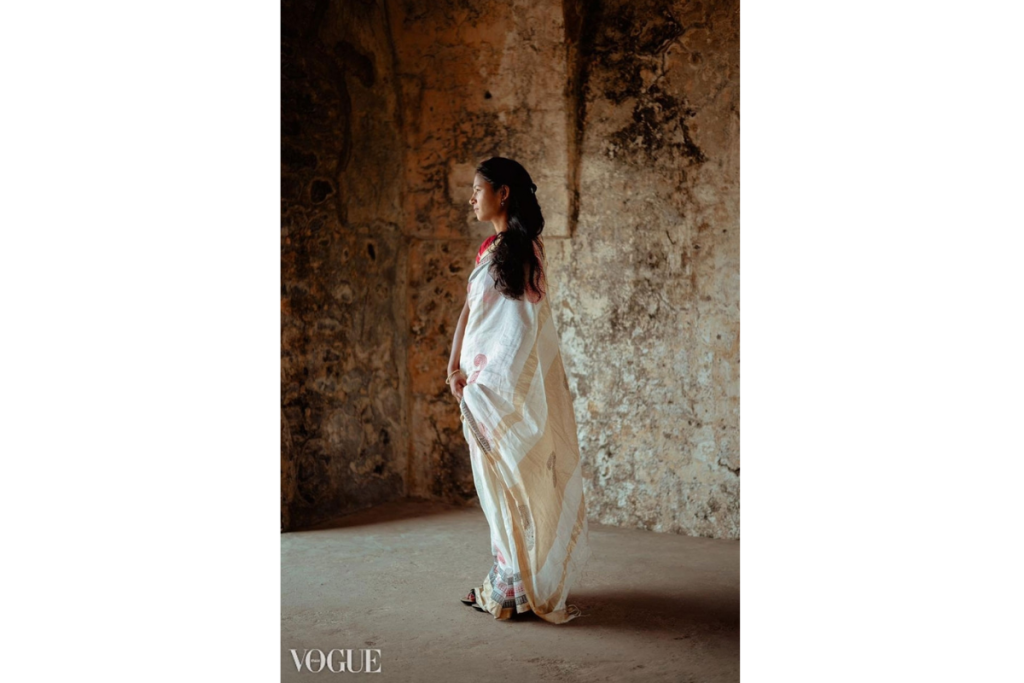
Mohammed Yusuf Khatri, in particular, has made significant contributions by training non-Khatri artisans in block-carving and printing, expanding the design repertoire, and introducing Bagh prints gararas, stoles, and home linens to a wider market. The Bagh print was also showcased in Vogue Italy and Harper’s Bazaar India. With its well-deserved Geographical Indication status and growing recognition in the global market, Bagh print is a story of great resilience showcased by one particular family and the beautiful design repertoire they embellish the cloth with. The narratives/symbols and elements encrusted in a Bagh cloth are examples of great visual art and display of stunning regional Bagh print motifs.
Image Courtesy – Bagh Print
Threads of Tradition: Tracing India’s Design Legacy from Ancient Textiles to Modern Narratives
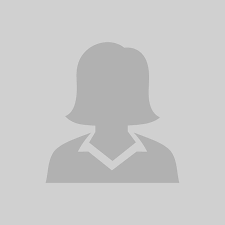
Contributor