Introduction
Few innovations in the field of contemporary innovation have aroused as much curiosity and expectation as 3D printing. 3D printing, also known as additive manufacturing, is a break from conventional production techniques and represents a paradigm change towards accessibility, efficiency, and customisation. Fundamentally, 3D printing offers unmatched design flexibility and low waste by enabling the layer-by-layer construction of three-dimensional objects from digital designs. To understand the complex workings of 3D printing, we will take a close look at its foundational ideas, technological developments, and wide range of industrial applications in this essay. We hope to shed light on the enormous effects of 3D printing on our environment and its revolutionary potential through this investigation.
Fundamentals of 3D Printing
The fundamentals of 3D printing lie in its unique approach to manufacturing, diverging from conventional subtractive methods to embrace an additive approach. Unlike traditional manufacturing processes that involve carving or molding material from a solid block, 3D printing builds objects layer by layer from digital designs. At the heart of this process is the utilisation of computer-aided design (CAD) software, which enables the creation and customisation of intricate three-dimensional models. These digital blueprints serve as the foundation for the additive manufacturing process, dictating the precise dimensions and specifications of the final object.
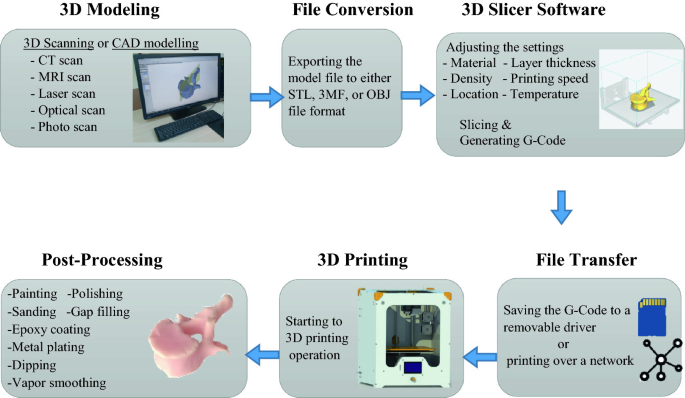
Once a digital model is prepared, it undergoes a process known as slicing, where specialised software divides the model into thin horizontal layers, akin to slices of a loaf. Each layer is then translated into a series of instructions that guide the 3D printer in depositing material precisely according to the design. This additive approach allows for unprecedented freedom in design, empowering manufacturers to create complex geometries and intricate structures that would be challenging or impossible to achieve through traditional means.
The actual printing process begins with the preparation of the 3D printer and the selection of suitable printing materials. Common materials used in 3D printing include thermoplastics like PLA and ABS, metals such as steel and titanium, and resins for specialised applications. The chosen material is heated or liquefied to a semi-fluid state and extruded through a fine nozzle, akin to a precision-controlled hot glue gun. The printer’s extruder moves along the designated path dictated by the sliced model, depositing successive layers of material to gradually build up the desired object.
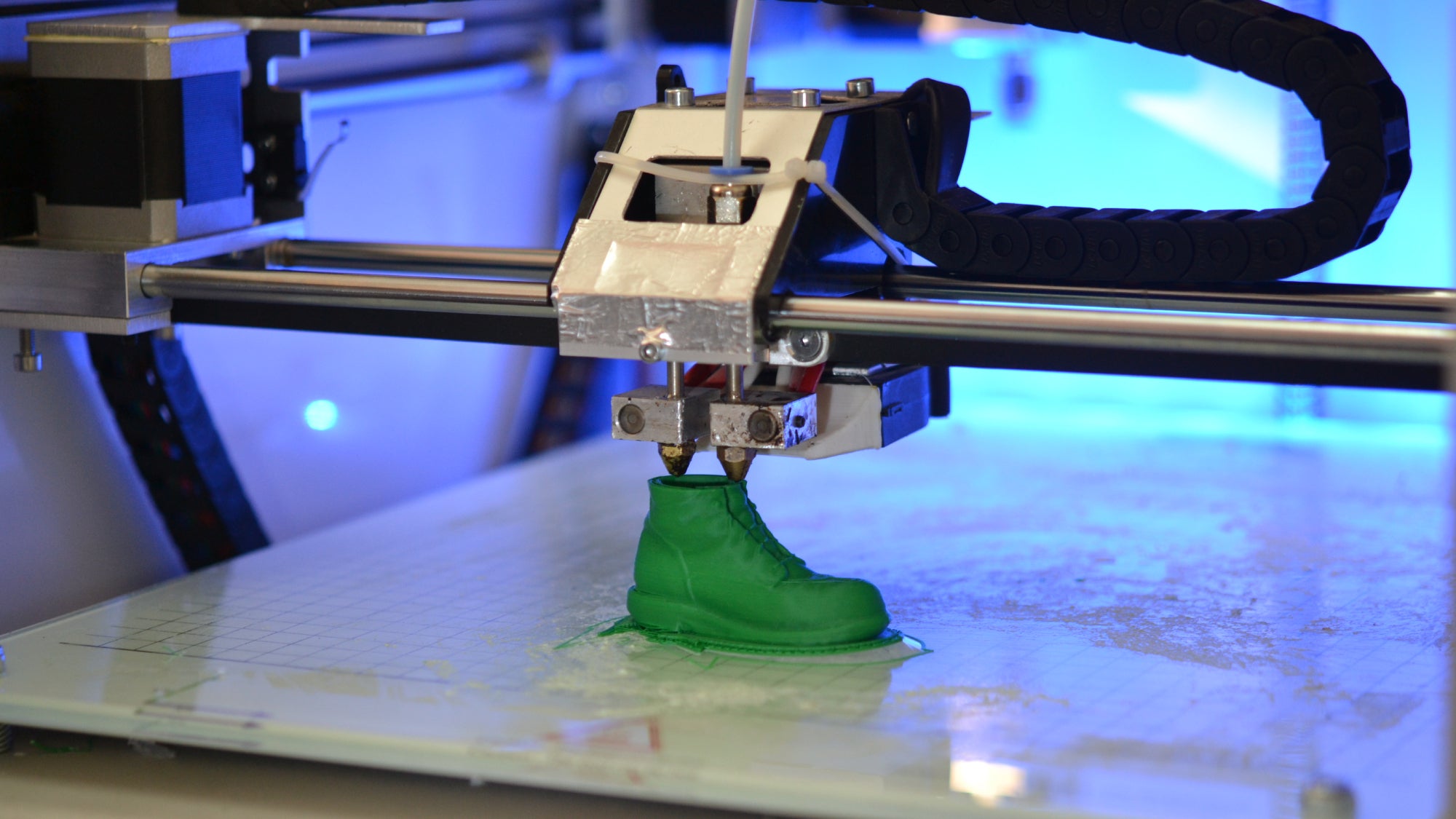
Layer by layer, the object takes shape, with each new layer fusing seamlessly with the preceding one to form a cohesive whole. As the printing progresses, support structures may be added to facilitate the creation of overhanging or complex features. Once the printing is complete, the object may undergo additional post-processing steps, such as removal of support structures, surface finishing, or curing in the case of certain materials like resins.
Anatomy of a 3D Printer
Materials in 3D Printing
Materials are the elemental ingredients that bring digital designs to tangible reality in the realm of 3D printing, dictating not only the physical characteristics but also the functional attributes of the final printed objects. The diversity of materials available for 3D printing encompasses a wide spectrum, ranging from thermoplastics to metals, resins, ceramics, and even biomaterials. Each material offers unique properties, advantages, and applications, empowering manufacturers to tailor their prints to specific requirements and achieve desired outcomes with precision and customisation.
- Thermoplastics:
- PLA (Polylactic Acid): Celebrated for its biodegradability, ease of use, and vibrant color options, PLA is a popular choice for prototyping, hobbyist projects, and consumer goods. It boasts a relatively low melting point, making it suitable for printers with standard temperature capabilities.
- ABS (Acrylonitrile Butadiene Styrene): Renowned for its strength, durability, and impact resistance, ABS finds applications in functional prototypes, automotive components, and engineering parts. It requires a heated print bed to prevent warping during printing.
- PETG (Polyethylene Terephthalate Glycol): Combining the best of PLA and ABS, PETG offers excellent layer adhesion, impact resistance, and chemical resistance. It is commonly used for mechanical parts, enclosures, and food-safe applications.
- Metals:
- Titanium: Prized for its exceptional strength-to-weight ratio, corrosion resistance, and biocompatibility, titanium is favoured for aerospace components, medical implants, and high-performance applications.
- Stainless Steel: Recognised for its durability, hardness, and corrosion resistance, stainless steel is suitable for functional prototypes, tooling, and industrial parts.
- Aluminium: Valued for its lightweight properties, machinability, and conductivity, aluminium finds applications in automotive, aerospace, and electronics industries for heat sinks, brackets, and structural components.
- Resins:
- Standard Resins: General-purpose resins offer a balance of strength, detail, and affordability, making them suitable for prototyping, jewelry, and figurines.
- Engineering Resins: Tailored for specific engineering requirements, engineering resins encompass a range of formulations such as tough, flexible, or heat-resistant materials ideal for automotive, aerospace, and healthcare applications.
- Dental Resins: Biocompatible resins designed for dental models, crowns, and surgical guides offer precision, accuracy, and biocompatibility required for dental applications.
- Ceramics and Composites:
- Ceramic Resins: Ceramic 3D printing enables the production of intricate ceramic parts with high temperature resistance and excellent surface finish, suitable for applications in aerospace, electronics, and biomedical fields.
- Carbon Fibre Reinforced Polymers: Combining the strength and stiffness of carbon fiber with the versatility of polymers, carbon fibre composites are used in automotive, sporting goods, and aerospace industries for lightweight, high-performance components.
Applications Across Industries
The transformative impact of 3D printing reverberates across a multitude of industries, revolutionising traditional manufacturing processes and unlocking new possibilities for innovation, customisation, and efficiency. From healthcare and aerospace to automotive and consumer goods, the versatility of 3D printing transcends boundaries, offering tailored solutions to diverse challenges and driving progress in countless sectors.
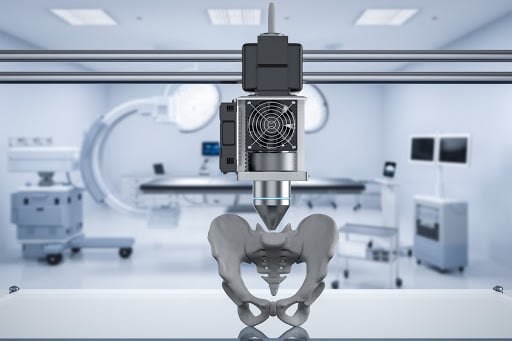
- Healthcare:
- Medical Devices: 3D printing enables the rapid prototyping and production of customized medical devices such as prosthetics, orthotics, and surgical instruments, tailored to individual patient anatomy for optimal fit and functionality.
- Bioprinting: Bio- printing technology holds promise for regenerative medicine and tissue engineering, allowing the fabrication of living tissues, organs, and scaffolds for transplantation, drug testing, and disease modelling.
- Surgical Planning and Training: Patient-specific anatomical models and surgical guides created through 3D printing facilitate preoperative planning, simulation, and training, enhancing surgical precision and patient outcomes.
- Aerospace:
- Prototyping and Tooling: 3D printing accelerates the development of prototypes, tooling, and fixtures for aerospace components, reducing lead times, costs, and material waste while enabling iterative design improvements.
- Lightweight Structures: Additive manufacturing enables the production of lightweight, complex structures with optimised geometries, enhancing fuel efficiency, performance, and durability of aircraft components and systems.
- Space Exploration: 3D printing plays a critical role in space exploration, enabling the on-demand manufacturing of spare parts, habitat modules, and propulsion components for space missions, reducing reliance on Earth-bound supply chains.
- Automotive:
- Customised Parts: Automotive manufacturers leverage 3D printing to produce customised parts, prototypes, and tooling with rapid turnaround times, enabling design iterations, performance testing, and cost-effective production of low-volume components.
- Supply Chain Optimisation: By decentralising production and enabling on-demand manufacturing, 3D printing reduces inventory costs, lead times, and logistics complexity, streamlining the automotive supply chain and enhancing flexibility in response to market demands.
- Performance Optimisation: Additive manufacturing allows for the creation of lightweight, complex geometries optimised for strength-to-weight ratio, aerodynamics, and thermal management, enhancing vehicle performance, efficiency, and sustainability.
- Consumer Goods:
- Customised Products: 3D printing empowers consumers to design and personalise products to their preferences, from jewellery and fashion accessories to home decor and electronics, fostering a culture of mass customisation and individual expression.
- Prototyping and Small-Batch Production: Designers and entrepreneurs utilise 3D printing for rapid prototyping and small-batch production of innovative products, enabling market testing, iteration, and customisation without the constraints of traditional manufacturing methods.
- Sustainability: By enabling local, on-demand production and minimising material waste, 3D printing promotes sustainable manufacturing practices and reduces environmental impact in the consumer goods industry.
Societal Implications and Ethical Considerations
References
- Xometry – Additive Manufacturing
- ScienceDirect – A review on 3D printing: An additive manufacturing technology
- IEEE Spectrum – Layer-by-Layer: The Evolution of 3-D Printing
- 3D Insider – Parts of a 3D Printer: List of Major 3D Printing Components
- The Ultimate 3D Printing Filament & Materials Guide
- Guide to 3D Printing Materials: Types, Applications, and Framework
- Built In – 18 Key 3D Printing Applications & Examples to Know
- Bioethical and Legal Issues in 3D Bioprinting – PMC
- Ethical challenges with 3D bioprinted tissues and organs – ScienceDirect
- 3D bioprinting and biofabrication – Journal of Medical Ethics
Feature image Courtesy: Olga Ilina/Shutterstock.com