What is a Dhabla?
Dhabla, a Rajasthani-style Kutch weaving, evolved through the migration of Vankar people from Rajasthan, settling in Kutch due to commerce. They mastered the unique dhabla weave suited to the region’s hot climate.The Meghwals’ journey to Kutch, driven by their devotion to Shri Ram Dev Pirji, added to the cultural tapestry. The Rabaris, sheep rearers and embroiderers, lacked weaving skills. Kutch’s earliest inhabitants, the Rabari and Ahir communities, engaged in sheep farming, but without weaving expertise. This convergence of cultures and crafts shaped dhabla’s heritage, with Vankar weavers playing a pivotal role in its creation and continuation.

Tracing its origins…
Originating in India’s Kutch region, Dhabla weaving epitomises desert elegance. Natural hues crafted the traditional 100-inch length Dhabla. Meticulously woven by Rabari women, it was a male hamlet’s classic blanket. Crafted from single/two-ply wool, the Dhabla was rain-resistant due to intricate patterning. Both practical and ornamental, it kept men comfortable. Cultural influences evolved the traditional Dhabla art. Vankar people of Gujarat’s state weave the fabric, unlike Ahir folks relying on agriculture. The Meghwals, despite being fewer, are famed for their bhojsari embroidery, crafting kashida pattu and Baladi checks.
Steeped in Tradition
Traditionally, the Dhabla was woven in two parts: a 26-inch width and a 100-inch length. Skillful Rabari women adorned it with intricate designs, donning it throughout the day. In ancient times, due to limited loom width, hand shuttles were used for the time-consuming weaving process, resulting in a heavy Dhabla. These blankets measured 80 to 100 inches in length. Rabari women, accompanied by goats and lambs, weaved Dhabla under the scorching sun for summer comfort. Local sheep’s wool was biannually harvested—pre-monsoon and winter. As demand grew, wool quality declined. Dhabla shawls adorned the wealthy, while the less fortunate wore them in rural settings.
Crafting a Dhabla
Crafted exclusively from wool, a vital necessity, the Dhabla weave proved more suitable for Rajasthan and Kutch winters than lighter cotton due to its regional availability. Goat and sheep wool formed the basis, woven using a pit shuttle loom and basic up-and-down technique. Traditionally, Rabaris gathered wool biannually from local sheep—before the rains and as winter concluded. Initially sufficient for local needs, rising popularity spurred demand, necessitating external yarn sources. Local wool lacked distinct attributes. Originating in Kutch, Gujarat, the Dhabla stands as a traditional handloom fabric. Skilled artisans weave two 26-inch sections meticulously, with women employing fine threads for careful stitching. Traditionally heavy due to single and two-ply yarn, its tight weave repelled rain. Both genders embraced the Dhabla for warmth and comfort.
Starting as shawls, the Dhabla catered to Rabari people in north-western Gujarat. Demand prompted the Rabari to diversify into international markets with sarees and stoles, employing various fibres alongside goat and sheep wool.
Weavers nowadays make use of four main types of yarn for their craft. The first is merino wool, which is consistently sourced from Ludhiana, India, and is acquired at the outset of November. However, its incorporation substantially drives up the cost of the final product within the local market. As a more budget-friendly option, artificial wool also finds its place. On the other hand, desi wool, originating from native sheep in the regions of Kutch and Rajasthan, provides a distinct material choice. Additionally, silks are also used from Bihar such as Tussar.
Dyeing of Dhabla
In the early stages of the industry, neutral shades like black, white, and brownish-brown wool were prevalent. As dyeing skills advanced, people began infusing colours into their sheep’s wool. Crafting a Bhujodi piece involves a sequence of steps: spinning, dyeing, warping, patterning, and weaving. These processes rely on time-honoured, essential tools. Recently, there’s been a resurgence of interest in organic dyes like blues, lac, and other natural materials for textile dyeing.The appeal of dyed wool has surged due to the increasing popularity of coloured fabrics. The demand for natural dyes sourced from items such as indigo, lac, and plant-based materials has made a remarkable return in the textile industry. Weavers use yarn in hanks, personally hand-dyeing them in small batches whenever they undertake the colouring process. Plant pigments have replaced animal-based ones in wool dyeing, embracing all-natural components like onion scraps, lac, and madder for producing vibrant vegetable colours.
/30-stades/media/post_attachments/SdtTfk6Ia2PgFbrEdkRu.jpg)
Spinning Process
Wool spinning is often undertaken by the weaver’s family, a role often fulfilled by women in Rabari communities. Subsequently, the weavers engage in fabric weaving. In the past, the traditional pit looms had limited width, allowing them to weave only half of a shawl at a time. This necessitated the stitching of the initial two halves together. An intricate fish stitch is utilised for this unique and appealing seam.Once the weaving is complete, the fabric is dispatched to dye houses. Following the dyeing process, the fabric is handed over to Rabari women, who enhance its aesthetic by skillfully embroidering it with vibrant and intricate patterns in various colours. Historically, animal shearing was the responsibility of herders until recent times. Periodically, shearers from neighbouring districts near the Rajasthani border visit villages to shear the sheep, a practice that continues once or twice a year.
Designs and Motifs of Dhabla
Artisans draw from their everyday routines to create traditional designs and patterns, often incorporating geometric motifs into their repertoire. Utilising the extra weft patterning technique they’ve devised, weavers can craft pointed motifs, though the method doesn’t lend itself to precise curvilinear patterns. While designers once favoured simplicity in their layouts, the prevailing trends now encompass general jaal patterns and designs rooted in basic geometric forms. Additionally, stripes that traverse the warp in the opposite direction are a consistent element.
Colour Schemes in Dhablas
The original dhabla’s colour palette was limited to natural dye shades like white, black, red, and brown. The remaining colours were more intricate in their arrangement. This white attire featured weft patterning in shades of black and burgundy adorning the sleeves and hem. Along the woven warp, black and maroon borders occasionally found their place. Predominantly, a scarcity of patterns characterised the overall aesthetic during most instances.

Revolutionising the Dhabla
Over time, this traditional art form has evolved significantly, embracing innovation and change. Initially, weavers utilized pit looms, accommodating only one weaver at a time. Following the 2001 earthquake, frame looms took the place of pit looms. Weft insertion techniques have also transformed, with fly shuttles supplanting hand shuttles. This shift has enabled the creation of wider fabrics, resulting in enhanced weaving speed. While the earthquake brought substantial losses, artisans recognize it as a hidden blessing that propelled the craft forward, even yielding distinctive warp side stripes.

Reviving the Craft…
Craft revival owes credit to governmental bodies, numerous non-governmental organisations (NGOs), and designers. Collaborative efforts have led to the adoption of finer reeds, cotton, silk, and insights into prevailing market trends. The weavers, guided by designers, have broadened their product range beyond shawls and blankets.Refinements are evident in yarn counts and elaborate patterns, with intricate embroidery now gracing the body along with borders. The colour palette has also adopted a contemporary flair.
During Covid-19, certain Dhabla weavers collaborated with students of NIFT to created new designs of Dhabla for the market, with such collaborations came new and vibrant creations that helped the craft stay afloat even during rough times. It gave a chance to the students to learn how to make craft and for the artisans to sustain their craft and inject some new life into their designs.
/30-stades/media/post_attachments/NBL8zcRDsTb0yoLXB70C.jpg)
Weavers now engage in weaving from September to February’s end, venturing across various Indian regions and states. Participation in prominent craft fairs such as Surajkund Crafts Mela and Virasat enhances their exposure to buyers and market dynamics. Focused primarily on the northern Indian market, these artisans intentionally create distinctive designs to avoid unnecessary competition amongst themselves. Additionally, numerous NGOs in the Kutch region foster connections with weavers, collaborating with esteemed fashion institutes like the National Institute of Design (NID) and the National Institute of Fashion Technology (NIFT) to provide guidance. These NGOs also conduct short-term training programs. Pricing of dhabla weaves hinges on the intricacy of extra weft patterning. The more intricate the patterning, the greater the labour and time investment, thus influencing the pricing structure.
Dhabla weaving stands as a unique illustration of exquisite handloom craftsmanship that needs to be continued and preserved and has every right to be known and worn by the people in this country and abroad.
Stories Stitched in Time: Chamba Rumal, The Needlework Wonders of Himachal
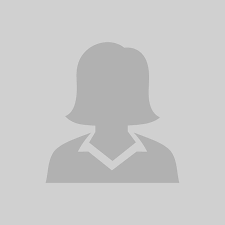
Contributor