Abhivyakti Shandilya
The art of Blue Pottery is a true marvel, born from a marriage of tradition and innovation. Its enchanting name stems from the mesmerising hue of cobalt blue dye that graces its surface, capturing the eye and stirring the soul.
This art form is unlike any other, for it eschews the use of clay, instead utilising a unique blend of quartz stone powder, powdered glass, Multani Mitti (Fuller’s earth), borax, gum, and water. The resulting material is a delicate and refined substance, yielding pottery of breathtaking beauty and exquisite craftsmanship.It was during the reign of Sawai Ram Singh II that Blue Pottery found its way to Jaipur, taking root in the hearts and minds of the people. Since then, it has become a treasured part of the city’s rich cultural heritage, delighting visitors with its intricate patterns and captivating colors.
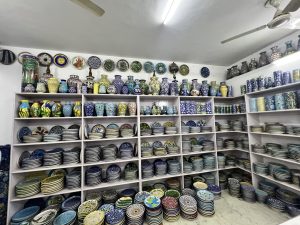
Courtesy:Abhivyakti Shandilya
The raw materials used like quartz stone powder, powdered glass, Multani Mitti (Fuller’s earth), borax, gum and water are ground in a traditional grinder called chakki. Then they are weighed and fixed in proportions. Then they are blended and kneaded with water and are available in the form of dough which is kept in a plastic bag to retain moisture. The dough is then flattened with a traditional tool known as thepai. The dough is set into open moulds and the edges are trimmed with a knife. Then these moulds are filled with ashes so that deformation does not take place and once it is set, the ash is removed and the mould is lifted. The sides are smoothened manually and it is polished with the help of sandpaper.
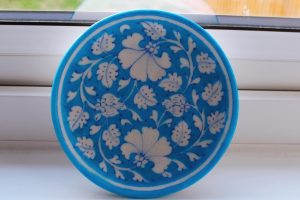
Courtesy: Abhivyakti Shandilya
Only the neck and lips are shaped on the wheel and the rest of the decoration and ornamentation is done with the help of a brush made from the hair of squirrels. All the items made by this technique are semi-transparent and are mainly designed by intertwined flowing patterns scattered with motifs of birds and animals. There is a wide range of products which are obtained by this method – urns, pots, vases, tea cups, plates, glasses, jugs, ashtrays and napkin rings. The most common colour used is blue which is derived from the oxide of cobalt, green from chromium oxide, turquoise from copper sulphate, yellow from cadmium oxide, and brown from iron oxide.
To create oxide colours, coloured stones are ground using a stone grinder called a silbatta. Gum is added to this mixture to bind the colours together. The process of designing and painting is followed by glazing. The glaze ingredients are placed inside the kiln and dripped out into cold water from the bottom of the kiln. The glaze material, in the form of molten lumps, is collected and turned into a fine powder. This powder is then applied to the product, which is ready to be fired in the kiln.
The kiln is fired with the help of either wood or coal and maintained at a continuous temperature of 800 degrees Celsius for approximately 8 hours. Afterwards, the kiln is allowed to cool for a minimum of 3 days before the finished products are removed.
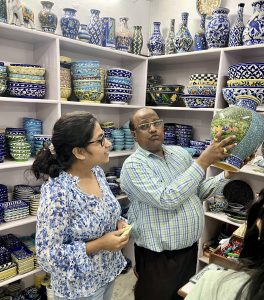
Courtesy: Abhivyakti Shandilya
Anil Doraya who is a National Award-winning artist and the owner of Jaipur Blue Pottery Art Cntre explains how Blue Pottery took an interesting route in finding its home in Jaipur. Ram Singh II attended a kite flying session and watched as his kite masters were engaged in battle with two brothers named Churaman and Kaluram from Achnera (Agra). When the ruler saw that the brothers managed to bring down the royal kites every time, he was intrigued. He asked the brothers their secret. Sawai Ram Singh II was impressed so he invited the brothers to stay in Jaipur and teach this unique form of glazed pottery at his new art school. Both were appointed heads of the department in the Museum and School of Arts. For the next 100 years, this department was solely under the control of their family. They told him that they were potters by profession and had coated their stings with the same blue-green glass that they used for their pots.
This splendid craft was kept alive and promoted by Highness Gayatri Devi and it experienced a sudden boost in the 1960s when the internationally acclaimed artist, Kripal Singh Shekhawat took an interest and joined the field of blue pottery. The impermeable and unique quality of not developing any cracks makes it an appropriate choice for everyday use. The craft is mainly performed by the Kharwal, Kumbhar, Bahairwa, and Nat castes. Of these, Kharawal and Khambar are the major producers of blue pottery.
Jaipur blue pottery is a unique and beautiful art form that has a rich history and enduring legacy. Its distinctive blue colour, intricate designs, and durability make it a popular choice for decorative items and a cherished piece of Rajasthan’s cultural heritage. Through the efforts of artisans and supporters, the art of Jaipur blue pottery continues to thrive and will undoubtedly continue to do so for many years to come.