Tracing its origins to the 19th century, this textile’s history is rooted in Chirala, situated along the coastal region of Andhra Pradesh. The term ‘Telia’ signifies oil, while ‘Rumal’ translates to handkerchief. Telia Rumal has stood as a pivotal Ikat tradition within Andhra. Its birthplace, Chirala, witnessed the initial emergence of these skills, the technique of creating telia rumals using double-ikat is predominantly nurtured in Telangana, with the village of Puttapaka emerging as a central production center.Referred to as chowka and Asia rumal, the telia rumal presents itself as a square textile. Its name, “oily kerchief,” originates from the pre-treatment of cotton yarn with an oil-based solution before weaving.
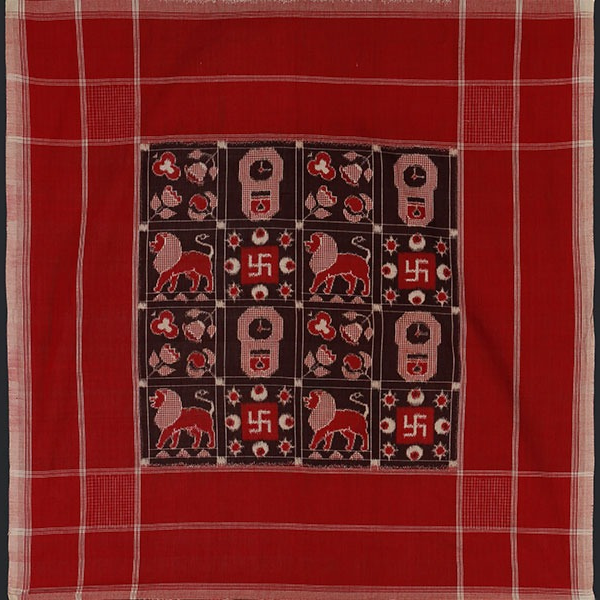
History and Resurgence of Telia Rumal
While historical records about the origin of the Telia Rumal technique are scarce, the recognition for unearthing this cherished artistry in the Nizam’s heartland belongs to Kamaladevi Chattopadhyay. A handful of years following India’s independence, Kamaladevi, renowned as a freedom fighter, entrepreneur, reformist, and feminist, was captivated by the understated elegance and adaptable appeal of a moistened towel elegantly wrapped around the head. Fueled by her fascination, she embarked on a journey to forge a fresh path in the realm of fashion.During the 1950s, weavers from Puttapaka crafted a versatile square textile with multiple applications, serving as a lungi, shoulder wrap, or even a turban. Kamaladevi’s influence spurred these weavers to channel their expertise into fashioning three sarees, for which she generously compensated them with 120 rupees. This pivotal act transformed the enigma of Telia Rumal and Ikat into a lasting chapter of history.
Tradings of Telia Rumal
In history, these rumals found their way to various destinations like East Africa, West Asia, and Burma, serving as lungis for local fishermen and cowherds. They also adorned men’s heads as turbans, with the oil infused during the dyeing process believed to offer protection from heat and dust. Refined Telia rumals, woven with intricate craftsmanship, graced the court of the Nizam of Hyderabad as dupattas worn by princesses. These were often adorned with embroidery or khadi work.The epicenter of production was the town of Chirala, located near the Andhra coast. From there, the technique radiated to Pochampally and nearby villages like Puttapaka. During the 1920s and 1930s, there was a transformation in motifs. Initially dominated by geometric designs, the patterns expanded to encompass figurative elements, even embracing contemporary symbols like airplanes and gramophones. As the mid-20th century approached, the production of telia rumals waned in Chirala due to a decline in global trade. However, the legacy persisted in Puttapaka and, to a lesser extent, in Pochampally.

Technique of Making Telia Rumal
Similar to the enigmatic origins of ikat weaving, the precise emergence of the telia rumal remains elusive in historical records, yet experts suggest its practice has spanned from the mid-1800s onwards. Comprising two uncut sections, each measuring between fifty-five to seventy-five square centimeters, the rumal showcases a broad, single-colored border encircling its primary field. This field is artfully divided into a grid adorned with recurring geometric motifs, while delicate checks grace the corner areas. The traditional palette of the telia rumal encompassed hues of black, red, white, and varying shades of brown, all achieved through the use of plant or mineral-based dyes.
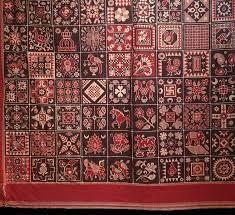
The creation of the Telia Rumal commences with the initial treatment of cotton yarn. The procedure involves soaking the yarn in a mixture of water and dung sourced from goats or cattle for a full day. Subsequently, the yarn undergoes treatment using a blend of Indian sesame oil (gingelly oil) or, on occasion, castor oil, combined with the ash extracted from castor-seed pods. The yarn is dipped in small quantities of this oil-ash fusion, meticulously worked upon for a duration of fifteen minutes, then gently pressed before being sun-dried. This sequence is repeated once daily for a total of sixteen days.

Once this intricate phase concludes, the yarn is thoroughly washed and dried. This series of steps contributes to the distinctive texture and fragrance of the telia rumal, which is the origin of its name. This stage also serves as a type of mordanting process, enhancing the yarn’s capacity to absorb dye effectively.
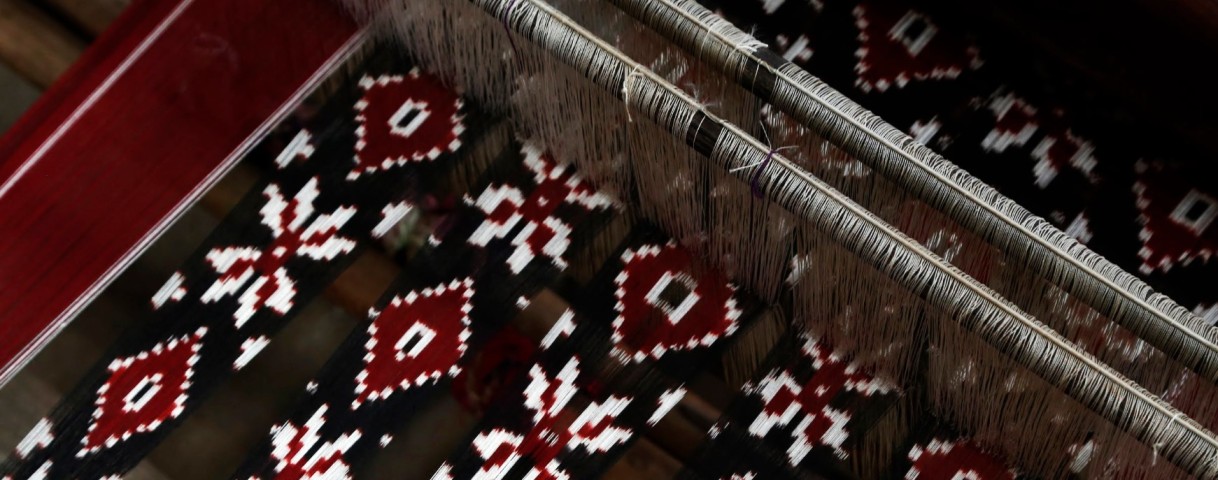
Moving on, the subsequent stage involves getting the warp and weft yarns ready. The yarn is meticulously wound onto cylindrical cones and then transported to a warping mill, a specialized apparatus that facilitates the precise measurement and arrangement of the warp yarn in the correct order. Similarly, the weft yarn is readied using a semi-circular frame. In earlier times, prior to the utilization of warping mills, the process of preparing the weft involved manual work on semi-circular wooden frames furnished with pegs, commonly referred to as “asu,” or occasionally on street-side poles.
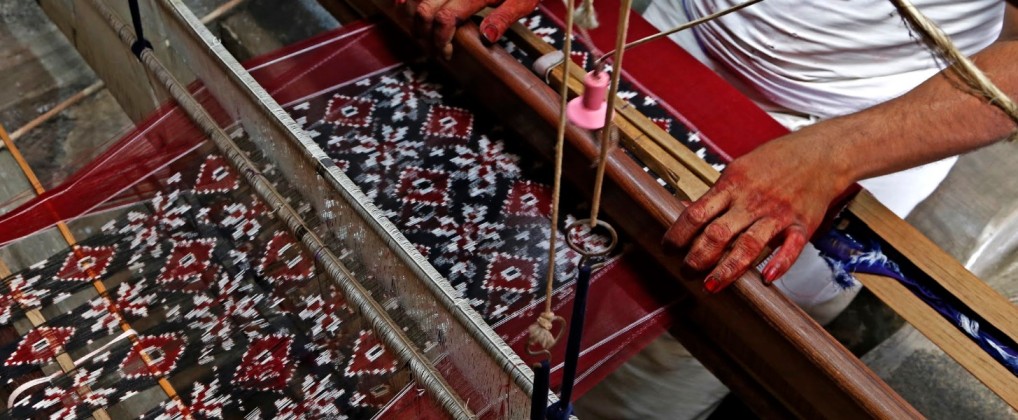
The telia rumal employs the double-ikat technique, where both the warp and weft are dyed using a resist method before weaving. To manage the intricacies of this technique, the design is initially charted on a graph. The weaver then approximates the number of threads per square inch, which hinges on the yarn’s thickness. Based on this calculation, the warp yarn is divided into units and secured.
Subsequently, the warp yarn is folded, allowing for the tying of around eight to ten rumals at once. With the guidance of a reference string, the design is transferred onto these yarn units. The portions of the warp and weft designated to resist dyes are fastened using strings or rubber ties. The weft yarns are subjected to dyeing only after the warp is situated on the loom. Once wound onto a tool called an “asu,” the weft yarns are stretched, marked, and dyed to match the design. Following this, the weft yarns are wound onto bobbins to be ready for the weaving process. Traditionally, a fly shuttle pit loom takes center stage in weaving the telia rumal.
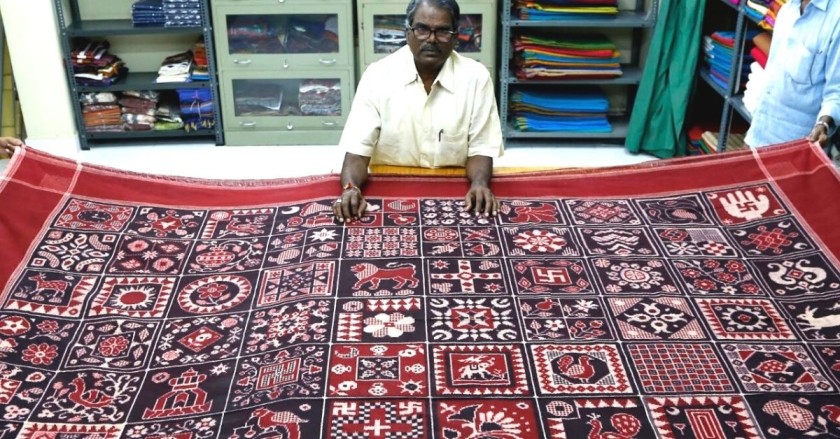
In modern times, the telia rumal has transformed beyond its traditional style and now adorns sarees, dupattas, and stoles. This evolution began around the 1950s. Although cotton yarn remains a staple in its weaving, materials like mulberry silk, tussar, and mercerised cotton have also found their way into the process. The resurgence of telia rumal weaving owes much to champions of revival such as Kamaladevi Chattopadhyay and others including Suraiya Hasan Bose and Martand Singh. Master weavers like Gajam Govardhana played a pivotal role, showcasing their handcrafted works internationally during the 1980s and 1990s through Festivals of India. Govardhana took the initiative to secure a Geographical Indications (GI) tag for the weavers of Puttapaka, which was successfully granted in early 2020, formally recognizing the significance of telia rumal. At present, the Telia weave predominantly graces sarees, there’s a rising trend in the popularity of Telia dupattas and stoles. Additionally, these fabrics are finding new applications as table covers or decorative wall hangings. The versatile nature of Telia fabric seamlessly aligns with the concept known as “fusion wear.”
Ms Laila Tyabji: Reviving and Reinventing Indian Handicrafts Through Dastkar initiative
However, there appears to be a shift in dynamics. There’s a substantial demand for Telia, but the challenge lies in its availability. Presently, very few weavers are engaged in crafting this style. Adding to this concern is the fact that the younger generation is opting to move away from this traditional craft. This sentiment resonates across the homes of many weavers at Nalgonda. Now, Telia rumal is being made on Powerlooms, further taking away the livelihoods of the few artisans engaged in the practice. Fortunately, there’s a growing support network comprising both individuals and organizations rallying behind the Telia Rumal. Notably, Microsoft is in the process of showcasing the Telia Rumal in a forthcoming coffee-table book dedicated to the fading art forms of Telangana. Additionally, the resurgence of interest in handloom is significantly propelled by the reach of social media platforms. Last year, for instance, the Telia saree garnered attention through multiple features on the #100sareepact blog, initiated by Ally Matthan and Anju Maudgal Kadam.Many artisans and weavers who had left the occupation in search for other better paying jobs are also now returning to the craft.

The Telia Rumal, a remarkable handwoven textile, has evolved from its traditional roots to grace modern fashion as sarees, dupattas, and more. Though facing challenges due to limited weavers and changing interests, the craft has found renewed hope with support from entities like Microsoft and the amplification through social media. This exquisite artistry stands as a testament to Telangana’s heritage, and its resurgence promises a brighter future for both artisans and aficionados alike.
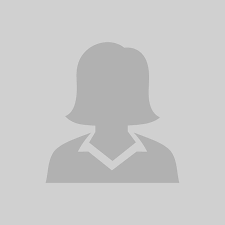
Contributor